Over the past four and a half decades, our primary focus has been on quality. We hire top talent, develop robust processes, and leverage advanced technology to maintain our position as an industry and global leader. Our production processes utilize the latest proven technologies in CNC machine tools, inspection equipment, cutting tools, and communications to eliminate waste, control variation, and create products of reliable quality.
It is Basin Precision Machining’s mission to provide unmatched customer satisfaction by maintaining a highly skilled staff who provide excellent customer service and innovation to create maximum value to our customer.
Lean Manufacturing and Continuous Improvement
Basin Precision Machining has been committed to lean manufacturing since the introduction of “the Goal” in the early 1980s. At Basin, Lean is a journey of continuous improvement.
We manufacture parts to exacting requirements by adhering to the principles of our in-house, ISO 9001:2015 certified Basin Business System. Our engineering, quality, and production staff work together as a team to ensure that we meet or exceed expectations.
View our ISO 9001:2015 certificate »
Corrective and Preventive Actions (CAPA)
These are implemented in response to a suspected deviation from one or more of the Basin Quality Systems. Utilizing 8D and 5-Why methodology, we have an analytical approach to problem solving. Work-flowed through our ERP system Plex, we never miss a step.
Statistical Process Control
The most current statistical methods are used to analyze our processes, assuring the highest quality product is produced and the robust, repeatable manufacturing process chosen remains stable and unchanged. Advanced process planning including Process FMEA and full PPAP submission are available to guarantee a smooth start up to the most difficult projects.
SPC data is recorded into Plex right in every work cell which parametrically links the data to the serial number of the material lot the measurement came from. This provides strong traceability, and the ability to track down issues with 100% certainty.
Measurement systems
Basin deploys seven Zeiss Coordinate Measuring Machines to assure access to accurate, timely, and automated measurement data to our team members. We also have vision systems, and a vast array of state-of-the-art manual measuring equipment.
Read more about our precision inspection equipment »
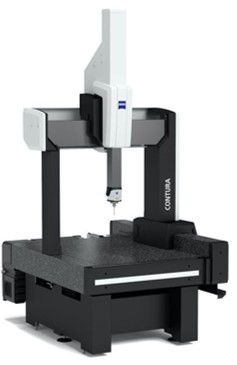
Industries Served:
Defense • Motorcycle • Hydraulic Components • Agriculture • Aerospace • Heavy Equipment

Locations:
Jefferson, WI Location
211 Collins Road
Jefferson, WI
920-674-6003
Your Solutions
We are...
State-of-the-art
Our proprietary software, Total Tool Maintenance TM™ (TTM™), Automation in Manufacturing™ (AIM™), and Scheduling System provide the data and information we need to produce quality parts, on-time.
We are...
Working smarter, not just harder
Our Horizontal Machining Center capacity has been expanded with the addition of a Mazak Palletech Flexible Manufacturing System (FMS). One of the largest in the country, our system offers 6 500MM Horizontal Machining Centers, 120 pallets, and 348 tools per machine. We can now produce any mix of complex parts with zero setup.
We are...
Innovative
- Our teams have the resources to meet customer needs.
- FMS automation reduces setups and maximizes utilization.
- Thermal deburring processes for 100% burr free product.
- Coordinate measuring machines and a fully networked facility help teams quickly gather relevant, accurate information
© 2025 Basin Precision Machining • Privacy Statement • Terms of Use • Site Design: D2P Web Design
Jefferson, WI Location • Basin Precision Machining • 211 Collins Road • Jefferson, WI • 920-674-6003